Canvas Prints
Upload Your PhotoHow Do I Make A T-Shirt
DIY T-Shirt Printing: Unleashing Your Inner Designer and Entering the Fashion Fray From Home
From punk rock patches to message tees with a cultural splash, the great DIY t-shirt is a canvas for our statements, our souls, and our style. But how does this wearable art transition from a glint in your eye to a bold figure on your chest? More profoundly, how do you upgrade this passion for graphic tees into a full-fledged business that can stand out in a market teeming with the eclectic, the expressive, and the everyday comfort of a well-worn favorite?
Design to Dye For: Initiating Your DIY T-Shirt Project From Scratch
The Foundations and Essentials
Before you splash into the white tide of t-shirt creation, a grounding in the essentials is your first stitch. Quality t-shirts are the bedrock of your project, and understanding fabric, fit, and feel is crucial.
Choosing the Perfect Tee
Tees come in more flavors than a sorbet shop, each with its weight, weave, and wear. A cotton-poly blend offers a smooth surface for most printing techniques, while 100% cotton can lend a vintage, slightly textured finish ideal for the beloved ‘70s screen print effect.
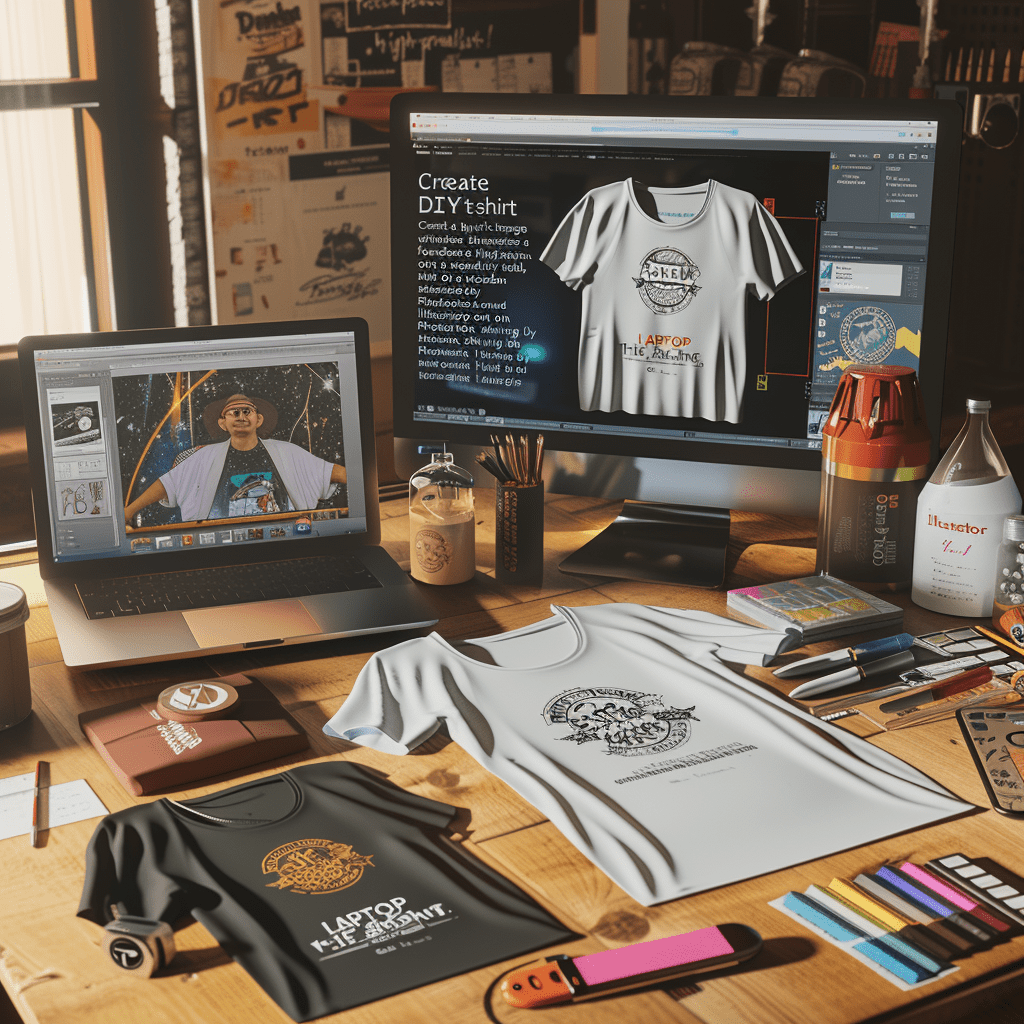
Knots and Bolts of Design Software
To weave your creative web, selecting the right software becomes paramount. Adobe Illustrator and Photoshop are the gold standards, offering a palette of tools and resources for image manipulation, text design, and scalable graphics which is essential for large format printing.
DIY Printing Methods Demystified
Screen Printing
A storied method requiring a stencil or screen for each color, screen printing is the darling of large batches due to its low cost per unit. This process offers impeccable, durable designs that can withstand countless washes, making it a go-to for band merchandise and brand logos. But, it's not for novices; the initial setup can be high, and the learning curve steep.
Heat Transfer Vinyl (HTV)
Imagine a vinyl sticker, but it stretches, and adheres permanently. HTV is user-friendly, especially for those familiar with cutting machines like Cricut or Silhouette, and offers a smooth, single layer finish. It's perfect for single shirts or smaller orders.
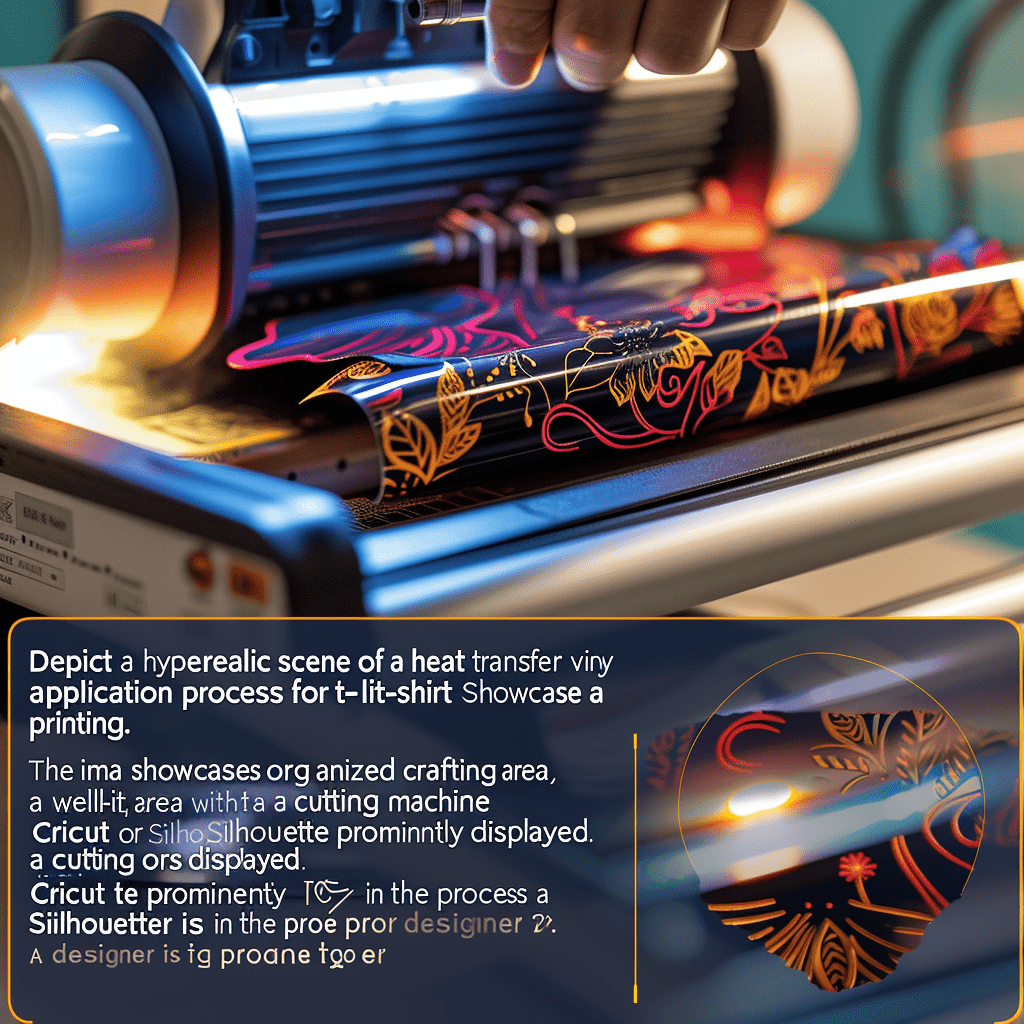
Direct-To-Garment (DTG)
DTG printing is akin to a high-resolution inkjet printer clapping out your design onto fabric. Although the service is often outsourced due to the investment in commercial-grade machines, the results are edge-to-edge prints with a satisfying soft touch, ideal for complex, multi-colored designs.
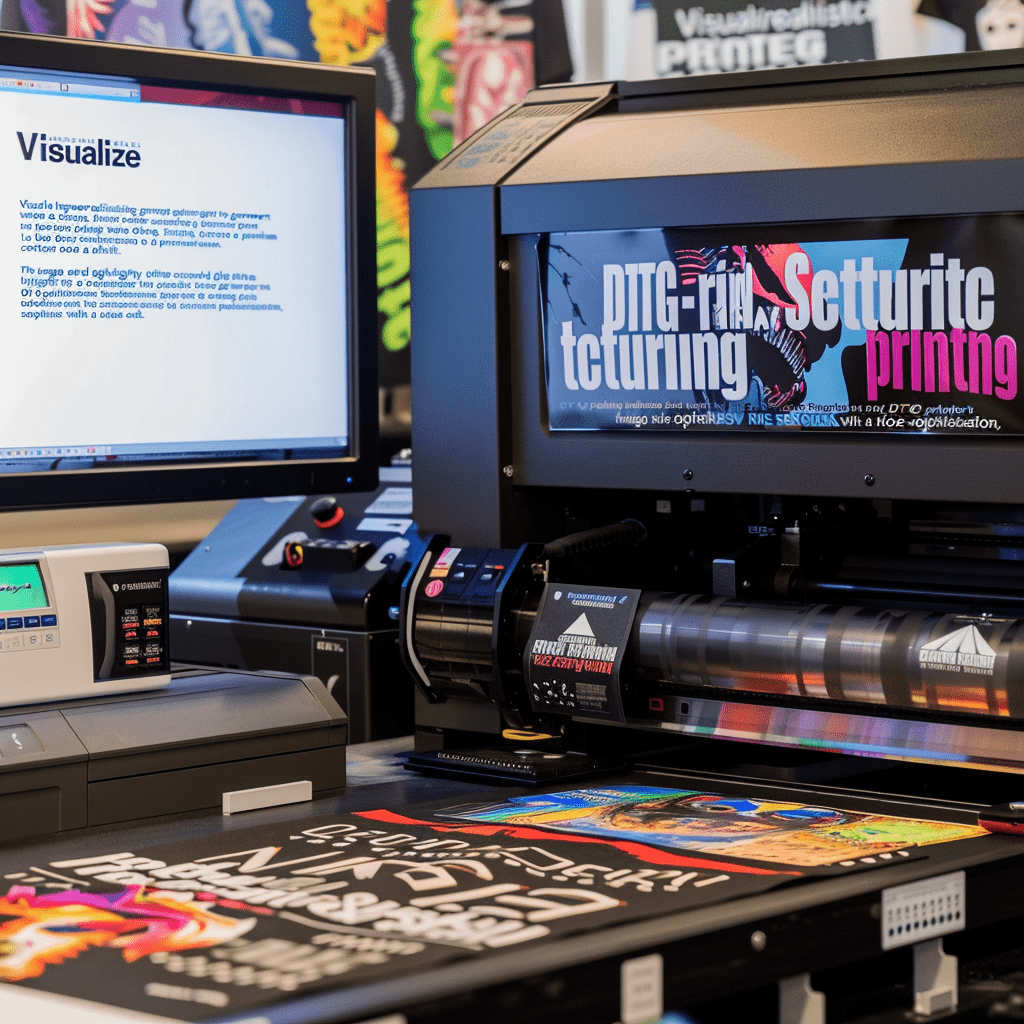
Common DIY Printer Pitfalls and How to Escape
The Blurry Border of Design
Fuzzy thinking meets fuzzy printing. Ensure your design’s resolution is high enough for a sharp print. 300 DPI (dots per inch) or higher is the golden rule.
The Heat Press Hassle
If using HTV, consistent pressure and the right temperature is your ticket to success. A heat press is a big boon, but if you're on a budget, pressing cloths with a nifty iron can do the deed.
Color Conundrum
The hues you see on your computer screen might not shake out the same on fabric. Calibrate your monitor for consistency and consider printing color guides or swatches to get an accurate read.
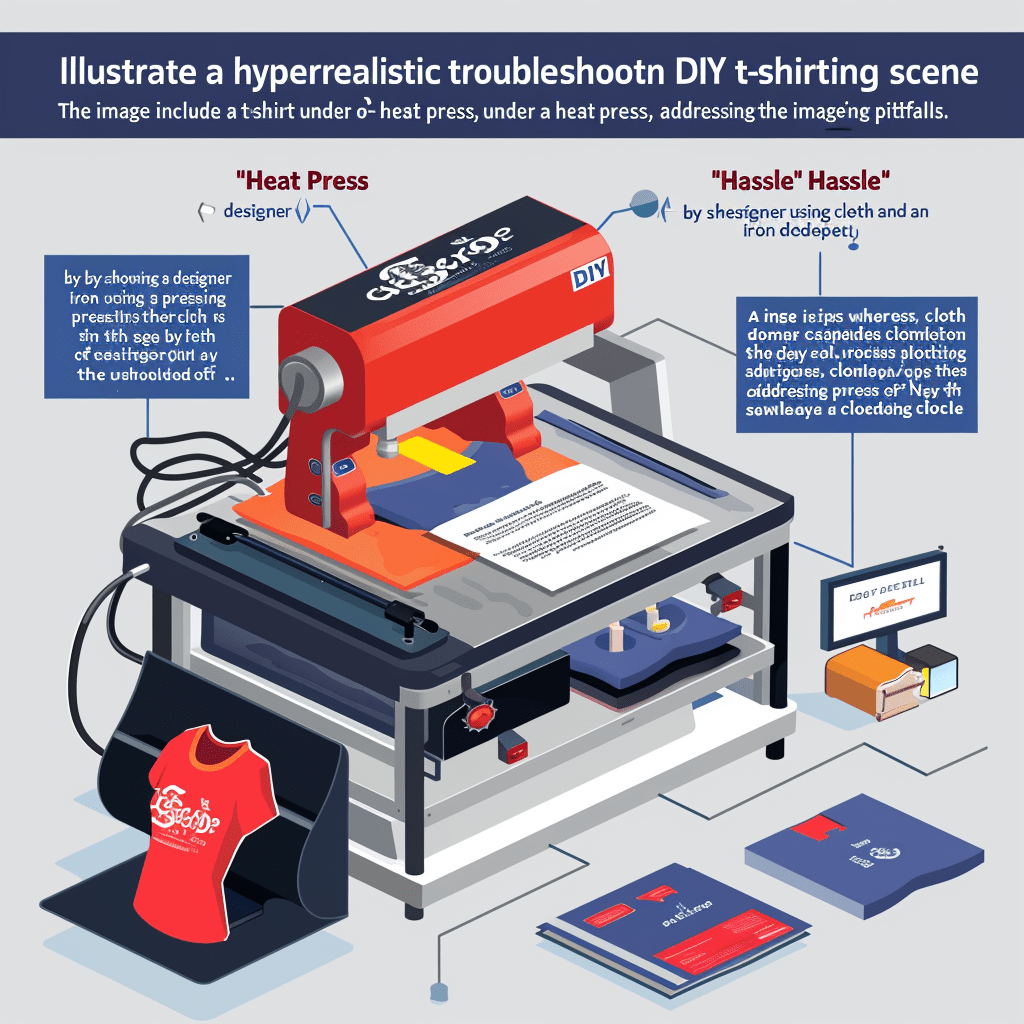
Beyond Basics: Honing Your Craft and Your Machine
From Beginner to Ballsy with Screen Printing
Getting Your Screen Right: Your design stands or falls on the frame - ensure your screen is tight and taut for even application.
Inks and the Spectrum Spread: Water-based inks are more eco-friendly but can lack in vibrancy. Plastisol ink, optimal for tees, brings the bang, offering vivid colors with durability.
The Squeegee’s Story: A squeegee not only clears the shower walls but also drives your ink into the fabric. Choose the right shape and durometer (the ink's degree of hardness).
DTG Printing: From Computer to Cotton
Taming the Textile Tiger: Pre-treat your garment to enhance vibrancy and wash fastness. This chemical treatment sets the tone for your inks.
Maintaining the Machine: Regular maintenance prevents print head clogging and keeps your machine spitting out sharp prints without a hitch.
Mastering the Art of Promotion and Selling
The Story Sells the Shirt
In the hum of the digital marketplace, a story sticks. Share your why - what makes your tees different? Who are they for?
Turning Clicks into Sales
Optimize your online storefront with compelling visuals, clear pricing, and a simple, secure checkout process. Utilize social proof like reviews and sales figures to build trust.
The Delivery Dance
From the packaging to the tracking number, every step is a part of your brand experience. Make it personal, make it memorable, make it yours.
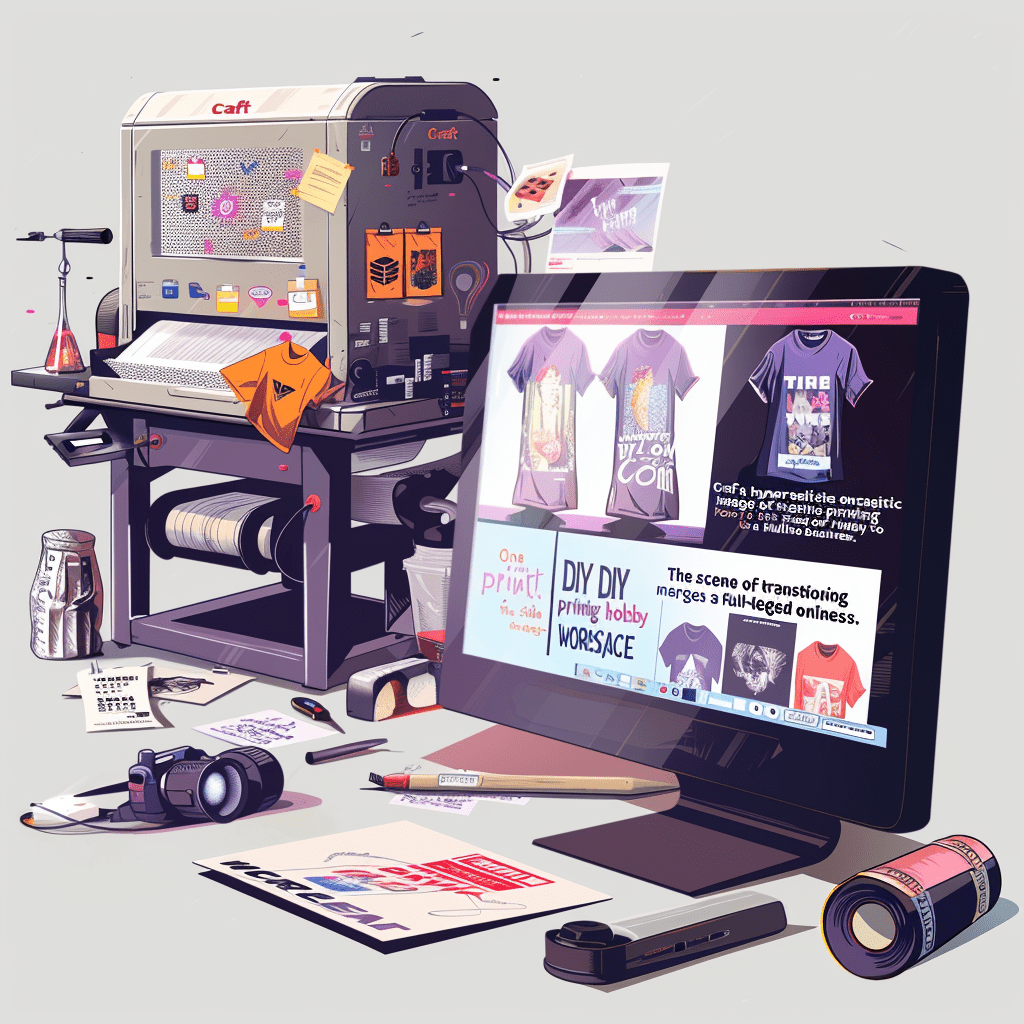
Leveraging Print-on-Demand for On-Demand Dreams
Take Stock in a World of None: With print-on-demand, inventory shifts to virtual; your designs are stocked only as digital files, ready to be printed on-demand.
Collaborating with Industry Giants: Teaming up with established print-on-demand companies not only avails you of their infrastructure but also their audience.
Quality Control in the Cloud: Choose print-on-demand partners diligently – your brand's reputation is in their hands. Check customer reviews, sample their wares, and stress-test their service.
Taking the Artisanal Turn with Iron-On Transfer Papers
The Paper Trail of Transformation
Choosing the Right Paper: For light or dark fabrics, the type of paper you choose is a pivot point. Light fabric transfer paper leaves no white background, perfect for those pastel designs. Dark fabric transfer paper is a touch thicker and includes an opaque backing, masking the fabric color beneath.
Preparing the Projects: Prior to printing, ensure that your designs are mirrored or flipped horizontally. This mirror image is vital for text and any designs with directional elements.
The Iron is Hot, and So Are You: Apply firm, even pressure with a cloth between iron and transfer paper. The duration depends on the brand, so follow the manufacturer's guidelines.
Iron-On Inspiration That Sticks
Design Matters Under the Heat: Complex designs with intricate details may not fare well with transfer papers, so simplify for the best clarity.
The Durability Dilemma: While iron-on transfers can last many washes, especially when cared for properly, they’re not as permanent as some other methods. Use the gentle cycle, inside-out, and avoid the dryer's heat.
Batch or Bust: Iron-on transfers are suited for the singular statement or a small batch; for larger volumes, other methods are more time-efficient.
The Stitching Together of a Legacy through T-Shirt Creation
The Thread of DIY: Each hand-pressed, hand-stitched t-shirt has a tale to tell. They're threads in the tapestry of our lives, imbuing our everyday wear with our personal narrative.
The Startup Seamstress / Seamster: Launching an online t-shirt business literally from your garage stitches together ambition, creativity, and commerce. It’s a story everyone’s excited to wear and share.
The Dye and Die of Traditional Techniques: Custom t-shirts have witnessed an evolution from tie-dye and stencil art all the way to today's digital prowess. The love for custom design remains, but the tools at our fingertips have shifted the brand of individuality we flaunt.
Navigating the Stormy Seams of T-Shirt Creation
Make It Last, Make It True: Quality craftsmanship backed by a fine story is your shield and standard. T-shirts that don’t just speak but shout your truth and talent resonate with a community of values, making the garment not just an article of clothing, but a cherished slice of self-expression.
Pricing in Passion: Deciphering the delicate dance of price is your ultimate test. Consider all the costs, from material to labor, but don't forget to value the intangible – your creativity and commitment.
The Tailored Technology Trend: Technology stitches us closer to our dreams, but don’t get lost in the software. At the heart of every tee is you, your vision, and your verve.
In sewing up your t-shirt passions, remember that even in the world of irons and inks, the most significant print you make is with your heart. Your story, your style, and your smile are the dye that colors the fabric of your potential. With each press and print, you're not just creating a t-shirt; you're crafting a legacy one stitch at a time.