Canvas Prints
Upload Your PhotoHow To Make Your Own Shirts
A Stitch in Time: Your Complete Guide to DIY Shirt Making
T-shirts aren't just a staple of casual wear, they're a canvas for the world to see the art you carry within. In an age where 'unique' is the new black, creating your own shirts has become more than just a pastime—it's a statement about your identity, your values, and your creativity. Whether you're an artist who wants to wear your designs with pride, an eco-conscious consumer looking to reduce your fashion footprint, or an entrepreneur with a vision for a thriving homemade T-shirt business, this comprehensive guide is tailor-made for you, pun very much intended.
In this exhaustive exploration of the DIY shirt making universe, we'll take a close look at every aspect of the process. You'll learn how to translate your grand T-shirt concepts into tangible cloth, discover the most up-to-date printing methods revolutionizing the DIY scene, and glean insights into navigating the digital landscape to bring your brand of shirts to the world.
It's time to roll up our sleeves, set up our sewing machines, and press the creative button, because we're about to immerse ourselves in the vibrant world of homemade shirts. Whether you're a newcomer to the art of fabrics or a seasoned pro looking for fresh inspiration, you’re in for a treat!
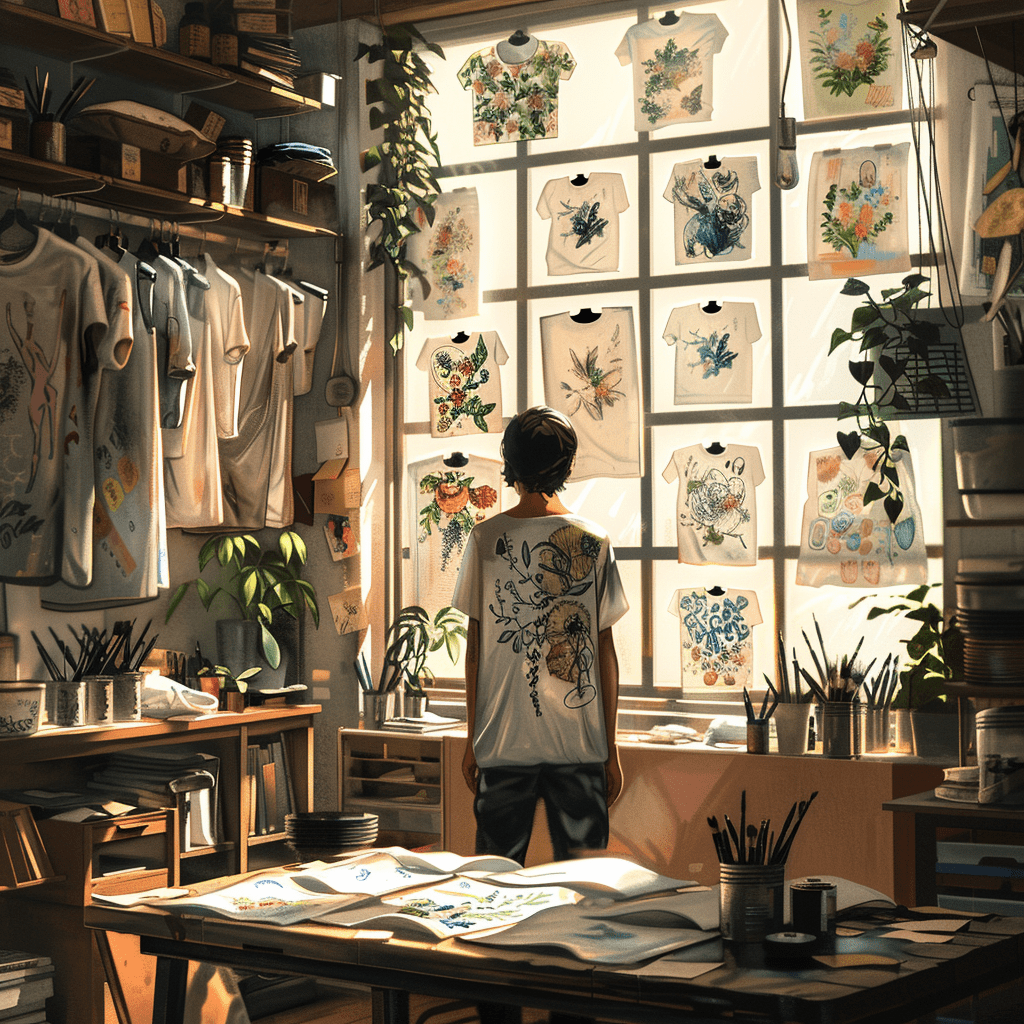
From Sketch to Stitch: The Creative Process of DIY Shirt Making
The t-shirt you dream of creating starts with the sketch on your notepad, the idea born from your musings, and a spark of artistic yearning. This section is dedicated to the dreamers and beginners—the ones who are standing at the edge of jumping into the vast and colorful ocean of shirt making.
Finding Inspiration for Your Shirt Design
Every great shirt has a story behind its creation. It could be an experience brimming with emotions, a cause close to your heart, a quirk of your personality, or simply a design that speaks volumes without the need for words. But where do you begin?
- Exploring Trends and Themes: Social media, websites like Pinterest, and even a walk around the block can expose you to a gamut of design styles and themes.
- Tapping into Personal Passion: The best designs emerge from a personal connection, be it your love for nature, a fascination with space, or an admiration for a particular art movement.
- Starting with Simple Graphics: If this is your maiden voyage, simple graphics or text designs can be a great way to dip your toes into the waters.
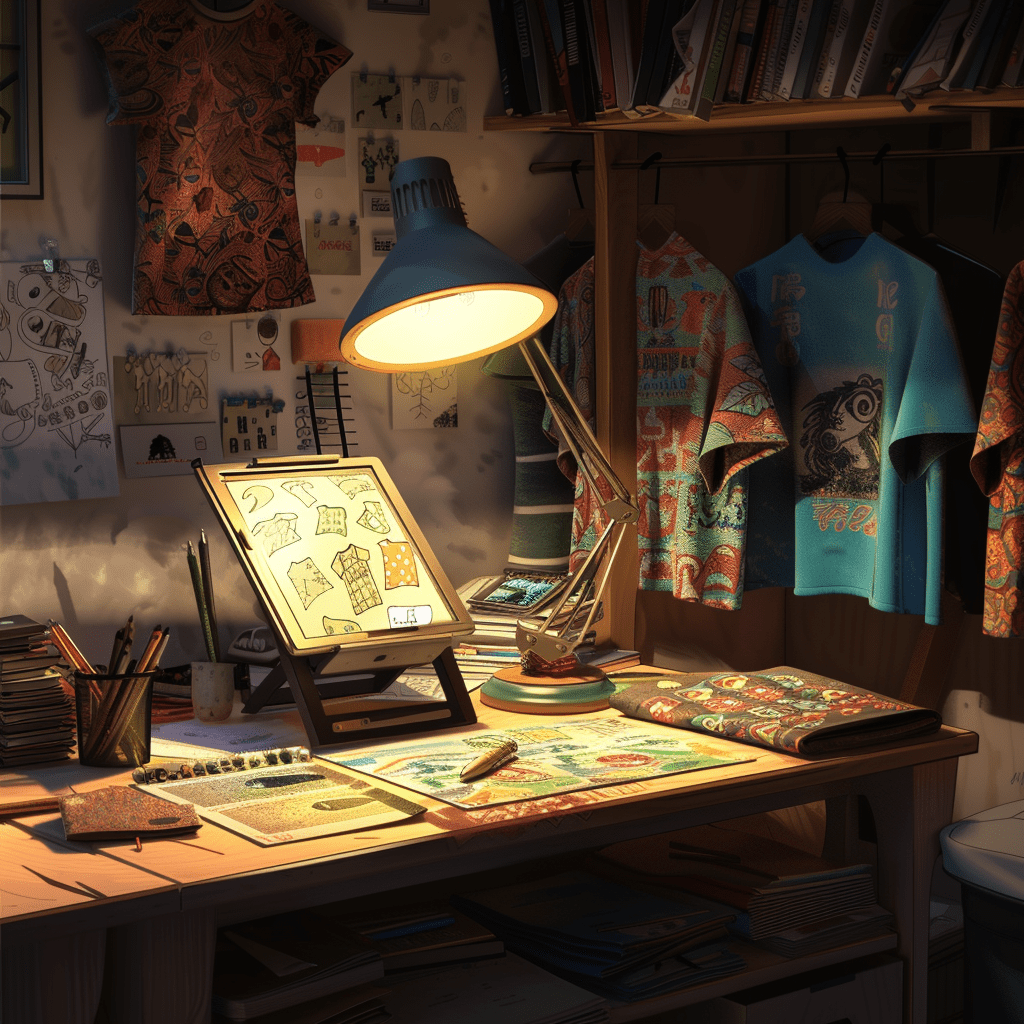
Making Your Vision Wearable
Once you have a clear idea of the design, the next step is to make it wearable. This involves considering the proportions, color schemes, and medium of the final delivery.
- Choosing the Right Color Palette: Color psychology plays a significant role in the effectiveness of your design.
- Understanding Shirt Types and Fabrics: The success of your design is impacted by the type of fabric and shirt cut you choose.
- Scaling for Shirt Size: A design that looks great on an A4 paper might need modification to fit comfortably across an XXL shirt.
Bringing Your Design to Life
You're nearly there—ready to turn your digital or hand-drawn masterpiece into a tangible item. The techniques for this are aplenty, from traditional screen printing to the modern marvel of direct-to-garment printing that brings intricate digital designs to life.
- Traditional Screen Printing: A labor-intensive but cost-effective method that works well for designs with few colors and requires a screen for each color in the print.
- Heat Transfer Vinyl: A method suited to small batches or single designs. It involves cutting the graphic out of a heat-transfer material and applying it to the shirt using heat and pressure.
- Direct-to-Garment (DTG) Printing: A newer, on-demand printing technology that operates like a traditional inkjet printer, directly applying the ink onto the fabric of the shirt.
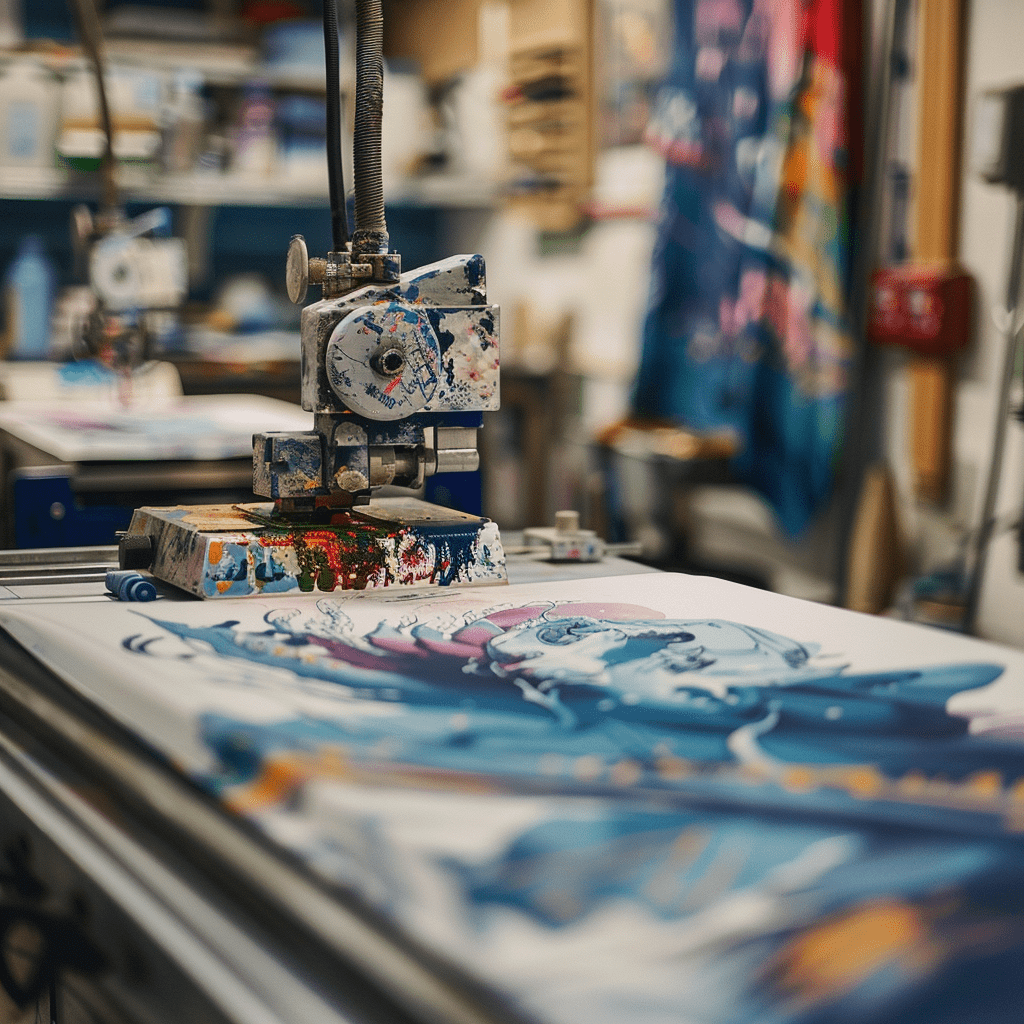
Imperfect Perfection: The Joy of Handmade Shirts
There's something undeniably special about shirts made with your own hands. It echoes a timeless tradition of clothing creation and imparts an extra layer of sentimental value to the garment.
- Sewing by Hand: If you decide to sew your own shirt, start with simple designs. Even basic stitches can create a profound impact with the right fabric choice and color combination.
- Hand-painted Designs: Fabric paint and brushes are your allies here. They allow you to create one-of-a-kind pieces, adding to the exclusivity and appeal of your finished product.
- Mixed Media Projects: For the adventurous spirit, combining fabric painting with embroidery or appliqué work can produce some truly unique and eye-catching results.
The Palette and the Press: Shirt Making Techniques Explored
The shirt-making landscape is a topography dotted with various printing techniques, each offering something unique. Whether you're looking for a cost-effective approach, a quick and easy method, or the best possible print quality, there's a method for everyone.
Screen Printing: The Time-Honored Tradition
Screen printing is to the DIY shirt maker what the potter's wheel is to the artisan potter—a classic. Born millennia ago in China, the technique has evolved to become a staple of shirt printing.
- The Process: A stencil (or screen) is created for each design color. Colors are applied in layers, with each layer requiring drying time before the next is added.
- The Pros and Cons: It's cost-efficient for large batches, yields vibrant color results, but can be complex for multi-colored designs and requires space and setup time.
Heat Transfer Vinyl: Where Simplicity Meets Precision
If you're looking for a method that balances print quality with ease of use, heat transfer vinyl could be your pick.
- The Process: Designs are cut into sheets of vinyl with a plotter. The sheet is then affixed to the shirt using a heat press or iron.
- The Pros and Cons: It's great for small batches, custom designs, and is relatively quick but can be more expensive and prone to peeling over time.
Iron-On Transfers: A Simple Portal to the Shirt Design World
The gateway method for many DIY enthusiasts, iron-on transfers, offers a straightforward way to get your designs onto fabric without a hefty investment or steep learning curve.
- The Process: Designs are printed onto special transfer paper. Under the heat of an iron, the ink is released from the paper and bonds with the fabric.
- The Pros and Cons: It's incredibly user-friendly, budget-friendly, and perfect for beginner designers. However, the results can look and feel like an "add-on" rather than an integral part of the fabric.
Direct-to-Garment Printing: Technology at Your Fingertips
For those who want to bring their digital art to life with impeccable detail and color fidelity, direct-to-garment (DTG) printing is the beacon of high-tech shirt making.
- The Process: A specialized printer applies the ink directly onto the fabric, much like a regular inkjet printer for paper.
- The Pros and Cons: It’s ideal for complex, multi-colored designs with fine details, allowing you to print on demand. However, it’s costlier per unit and has limitations on the fabric type and colors it can print on.
Designer's Delight: Software and Tools for Crafting Shirts
Every designer needs a canvas, and for shirt makers, that comes in the form of software and tools. Choosing the right mediums for your creative expression can make a significant difference in the final product.
Designing by Bytes with T-shirt Design Software
There's a range of software designed explicitly for creating shirt prints, each offering a mix of ease of use, design capabilities, and cost.
- Adobe Illustrator and Photoshop: Industry standard software with robust design features but comes with a learning curve.
- CorelDRAW: A powerful, vector-based design program that is particularly popular among screen printers.
- Online Services: Platforms like Canva and Designhill offer user-friendly, web-based design tools that require no installation and come with a plethora of templates and assets.
Physical Tools for the Hands-On Designer
Sometimes, the most intimate connection you can have with your design is through physical tools. Whether it’s a pair of scissors for fabric cutting or a set of brushes for fabric painting, these tools bridge the gap between your imagination and the tactile world.
- Cutting Machine: For designs that involve complex patterns or repeated motifs, a cutting machine like a Cricut can save time and ensure precision cuts.
- Paintbrushes: A variety of brushes for different strokes and techniques are your allies in painting designs by hand.
- Fabric Markers and Paints: These little tubes and pens of color are magical wands for the DIY shirt maker, allowing designs to shift from imagined to material.
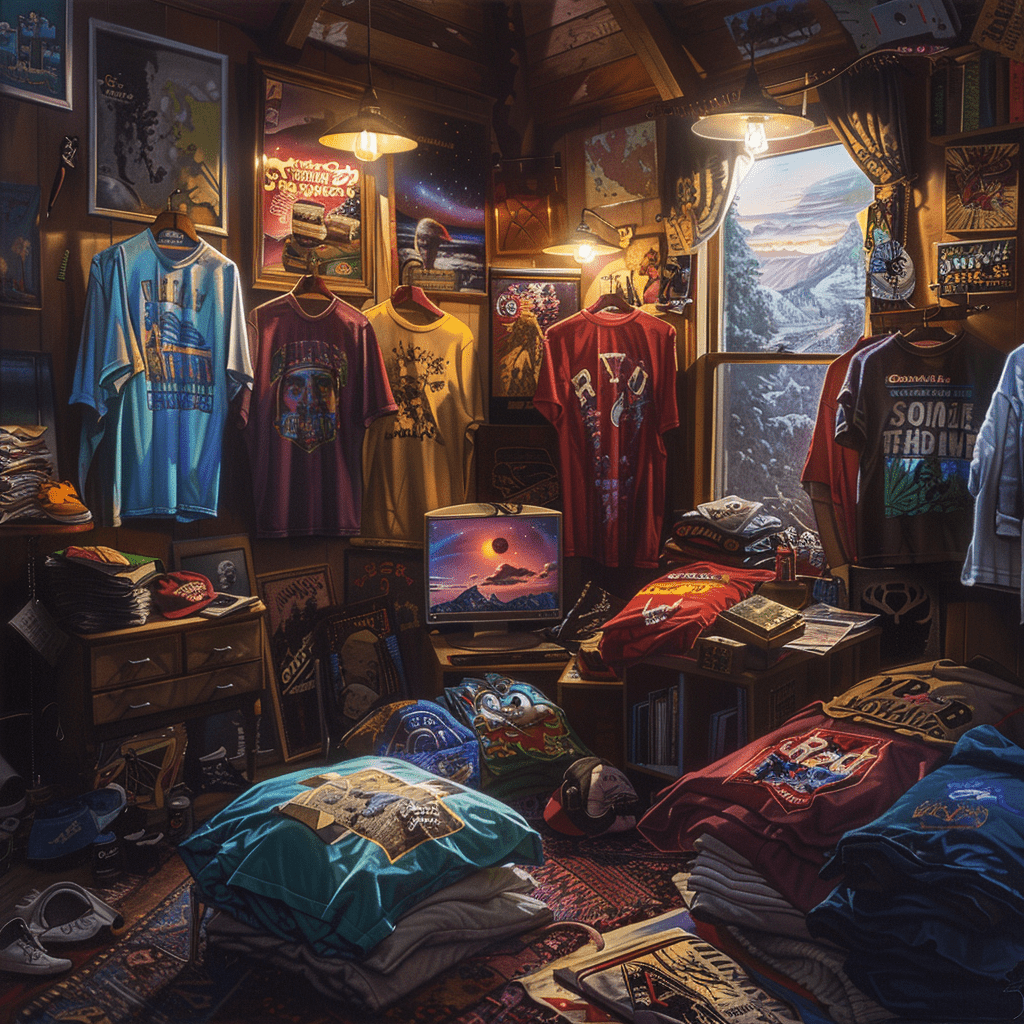
Incorporating Tech into Your Creations
Technology is not just changing the way we live; it's altering the fabric of the way we create. In the DIY shirt making domain, the integration of tech has opened up avenues that were once the realms of science fiction.
Taking Craft to the Cloud with Print-on-Demand Platforms
Print-on-demand (PoD) platforms are the perfect synthesis of technology and tradition, where you upload your designs, and they handle the rest—printing, shipping, and customer service.
- Ease of Use: Most PoD services offer user-friendly interfaces that make the design-to-shirt process straightforward.
- Wide Reach: These platforms give you access to a broad customer base, reducing the need for you to handle marketing and distribution.
- Customization Options: You can offer a variety of shirt styles, colors, and sizes without having to stock inventory.
Leveraging E-commerce to Sell Your Homemade Shirts
The e-commerce ecosystem has democratized the selling of homemade items, offering a global marketplace for DIY shirt makers to showcase and sell their creations.
- Building an Online Store: With platforms like Shopify and Etsy, setting up an online store is as easy as few clicks.
- Marketing Tools: These platforms provide tools to help you reach potential customers through online advertising, social media, and more.
- Community Building: You have the opportunity to build a community around your brand, engaging with customers, and fostering a brand identity.
The Road Less Embroidered: A Frontier for Custom Creations
The desire for custom, handmade items has given rise to a new kind of DIY shirt making—one that speaks less about mass production and more about craftsmanship.
The Allure of Hand-embroidery
Hand-embroidery brings a unique, artisanal touch to shirts. The imperfections and personal flair it adds can turn a plain shirt into a timeless piece.
- Selecting Thread: The choice of thread color and type can drastically affect the look and feel of your design.
- Patterns and Stitches: From a running stitch to a French knot, there is a plethora of stitches to learn and experiment with.
- Blending Techniques: Combining embroidery with other methods like patchwork or beads can open up a treasure trove of creative possibilities.
The Patchwork Path
Patches have held a symbolic and aesthetic value in fashion for centuries. They're a tribute to the adage “waste not, want not,” transforming worn-out shirts into new, unique pieces.
- Sourcing and Selecting Material: Patches can be cut from old clothes, bought from craft stores, or even traded with friends or fellow DIYers.
- Design Placement: The placement of a patch can be incidental or deliberate, offering an opportunity to play with shirt designs creatively.
- Attaching and Securing Patches: From sewing to gluing to ironing on, there are various methods to attach patches. Each has its own charm and challenge.
The Dye of the Tiger: Exploring the World of Fabric Coloring
Sometimes, a design demands more than just a print or a stitch—it craves color in a fluid, organic form. Fabric dye can offer a vibrant or subdued palette, allowing you to express your design in new hues.
Tie-dye Techniques: A Splash of Color and Rebellion
Tie-dye is more than a technique; it's a statement. It punctuates shirts with patterns that are as singular as the method of making them.
- Shibori: This Japanese tie-dye technique creates a signature soft-edged pattern, usually in indigo.
- Crunch Method: Achieved by scrunching a shirt and applying dye, it produces a starburst pattern when unfolded.
- Use of Colors: Experiment with everything from neon-bright, eye-searing colors to the mellow, understated tones.
The Dip-Dye Art
Dip-dyeing is a simple yet effective way to add gradients or blocks of color to a shirt.
- Color Selection and Mixing: Understanding color theory can help in crafting the perfect hues. Mixtures of dyes can also be used for unique shades.
- Orientation and Technique: The way you dip, and how far into the dye bath you go, will determine the final result.
- Post-Dye Treatment: Washing and caring for a dip-dyed shirt requires slightly different handling than a regular shirt, but the results are well worth it.
Sustainable Fashion Starts at Home
With sustainability becoming a growing concern, DIY shirt making presents an eco-friendly alternative to mass-produced clothing.
Choosing Eco-friendly Materials
Cotton is the most common material used for shirts, and organic cotton is an environmentally conscious choice due to its reduced impact on the environment.
- The Organic Promise: Grown without pesticides, organic cotton is kinder to the planet and those who farm it.
- Bamboo and Hemp: Shirts made from bamboo and hemp offer a sustainable and versatile alternative to cotton.
The Second-hand Renaissance
Give old shirts a new lease on life by upcycling or repurposing them.
- Reworking Existing Shirts: Add patches, embroidery, or dye to transform old shirts into new, personalized pieces.
- Sourcing Second-hand Materials: Thrift stores and online marketplaces can be treasure troves of materials for your DIY projects.
Care and Maintenance of Homemade Shirts
Your shirts are more than just clothes—they're an extension of your creativity. Caring for them properly ensures they can continue telling your story for a long time.
Laundering Tips for Longevity
Proper laundering techniques can help retain the vibrancy of colors and the integrity of the fabric.
- Hand Washing vs. Machine Washing: Hand washing is generally gentler on shirts but can be time-consuming. Using a washer's gentle cycle is a suitable alternative.
- Detergent Choice: Choose a color-safe, gentle detergent to wash homemade shirts.
- Drying Methods: Air-drying shirts can help prevent shrinkage and fading. If using a dryer, set it to a low temperature.
The Business of Making Shirts: Selling, Marketing, and Branding
If you've caught the shirt-making bug and are considering turning your passion into a business, there are several factors to consider beyond the creation process.
Developing Your Brand Identity
A memorable brand identity is crucial for standing out in a crowded market.
- Creating a Distinctive Logo: Your logo is the face of your brand. Ensure it encapsulates the essence of your designs and appeals to your target audience.
- Defining Your Niche: What makes your shirts different? Is it your design style, the shirt type, or a unique production story? Make that your niche.
- Crafting a Compelling Brand Story: The tale of your brand can resonate with customers on an emotional level, fostering loyalty and connection.
Marketing Your Homemade Shirts
In a world of infinite choices, marketing helps your shirts find their way to the people who'd love them.
- Utilize Social Media