Canvas Prints
Upload Your PhotoPrinting T Shirt
The Digital Canvas: Mastering Home-Based T-Shirt Printing
In an age where personal expression is as vital as the air we breathe, owning a piece of clothing that screams 'YOU' is an unmistakable luxury. T-shirts have evolved from mere garments to canvases of personal statements, and there's a thrilling ubiquity in the act of transforming a blank fabric into a wearable piece of art. For small business owners, graphic designers, and fashion aficionados, this evolution has opened a multitude of opportunities to design and produce custom t-shirts from the comfort of one's home.
In this comprehensive guide, we will explore the fascinating world of home-based t-shirt printing - from the tools of the trade to the nitty-gritty challenges and the horizon of innovation. Whether you're an aspiring entrepreneur looking to set up a micro-enterprise from your living room, or a hobbyist seeking to expand your craft, this content is for you.
The Tactile Art of T-Shirt Printing
T-shirt printing is a tactile art that blends technology with traditional craftsmanship. Understanding the various methods and their applications is crucial to achieving high-quality results.
Discover Top Printing Techniques
-
Screen Printing
Screen printing remains a classic method that champions vibrancy and longevity. Though it demands more setup, it's a preferred method for bulk printing due to its cost-effectiveness per unit.
- Vibrant colors that stand out
- Perfect for simple designs with solid colors
- Not ideal for complex designs with gradients
- Requires different screens for color separation, hence longer setup time
Helpful Tip: Invest in high-quality, durable screens to outlast multiple print runs.
-
Direct-to-Garment (DTG) Printing
DTG is the digital marvel that affords intricate details and gradients with ease. It's akin to printing a picture on paper, but the ink is led directly onto the fabric.
- Unlimited color options with intricate detail
- Ideal for small print runs and one-offs
- The price per unit can be high for bulk prints
- Requires pre-treatment for many fabrics, which can be time-consuming
Helpful Tip: Pre-treatment with care and precision ensures compatibility with various fabric types.
-
Heat Transfer Printing
Heat transfer printing involves applying heat to transfer an image onto the fabric. This method is adaptable and quick, making it a go-to for temporary designs.
- Quick and cost-effective for small batches
- Allows for a wide range of design types and styles
- The longevity of color vibrancy is lower compared to other methods
- Setup can be complicated for beginners
Helpful Tip: Understand and control the variables of time, temperature, and pressure to perfect your transfers.
-
Vinyl Cutting
Vinyl cutting is a precise method that transforms designs into shapes cut from sheets of colored vinyl. The cutouts are then heat-pressed onto the t-shirt.
- Durable and can last through numerous washes
- Great for lettering and monochrome designs
- Tedious for intricate multicolor designs
- Can be more costly for larger batches
Helpful Tip: Ensure your blade is sharp and your cutter is precise to avoid errors in intricate designs.
-
Sublimation Printing
Sublimation is a method that uses heat to transfer dye onto materials in a gaseous state. It's a process tailor-made for polyester fabrics, ensuring a permanent, high-resolution print.
- Virtually no feel to the print
- Long-lasting image durability
- Limited to light-colored garments
- Polyester-specific prints restrict fabric choices
Helpful Tip: Select your inks wisely, as not all sublimation inks are created equal in terms of color output and permanence.
The Do-It-Yourself T-Shirt Printing Guide
Turning your t-shirt concept into reality is more achievable than you might think. This DIY guide is the map that takes you from mere ideas to wearable expressions.
DIY Printing Equipment Essentials
- A Home Screen Printing Kit
- A Direct-to-Garment Printer
- A Heat Press Machine
- A Vinyl Cutter
- A Sublimation Printer
- Common Tools
Quality Considerations
- Font and Style Selection: Choose fonts and styles that resonate with your message and your audience.
- Image Quality: High-resolution images or clear line work translate into high-quality prints.
- Proper Sizing: Size your designs appropriately for the t-shirt area you intend to print.
- Material Choice: Different materials hold prints in different ways. Consider the end use of the t-shirt when choosing material.
The Do-It-Yourself Printing Process
- Design creation and prepping.
- Screen printing: Ink mixing and application. Printing with precision and care.
- Direct-to-Garment (DTG) printing: Pre-treating the fabric. Loading your design and printing.
- Heat transfer printing: Preparation and cutting of vinyl. Heat pressing your design onto the t-shirt.
- Sublimation printing: Printing onto sublimation paper. Transferring the design onto the polyester-based t-shirt.
The Art of T-Shirt Designing and Digital Printing
Designing a t-shirt is more than selecting colors and pictures. It's a balance of creativity and technicality that results in a wearable narrative.
The Creative Process
- Understanding the Message: What are you trying to convey? Be clear on the message you want your t-shirt to send.
- Conceptualization: Translate your ideas into a rough design. Sketch it out on paper or use digital tools for the first pass.
- Visual Appeal: Ensure your design is visually captivating. Play with layout, contrast, and spatial relationships to get it right.
The Technical Aspect
- Software Selection: Familiarize yourself with design software. Choose the one that aligns with your skills and budget, be it Adobe Illustrator, Photoshop, or free alternatives like Inkscape and GIMP.
- File Types: Understand the differences between file types, especially when it comes to printing. For example, vector graphics are scalable and maintain quality regardless of size.
- Color Considerations: Learn about color theory and how it applies to t-shirt design. Consider the color of the fabric and the palette of your design.
Tips and Tricks for Successful Home-Based T-Shirt Printing
Success in home-based t-shirt printing lies in the details. These tips and tricks will serve as your compass through the process.
General T-Shirt Printing Tips
- Test your prints on scrap fabric before making the final print.
- Keep detailed notes on each print, including variables like pressure, heat, and ink consistency.
- Regularly clean your equipment to ensure proper function and to extend its life.
Screen Printing Secrets
- Ensure your design is registered correctly on the screen to avoid misalignment.
- Use the right squeegee technique – it's more than just a push or a pull.
- Experiment with different inks to find the ones that work best for your design and fabric.
Direct-to-Garment Wisdom
- Invest in good pre-treatment machines to save time and ensure consistency.
- Opt for a printer with white ink capability for more design flexibility.
- Keep your printer calibrated and have it serviced regularly to maintain optimal performance.
Heat Transfer Mastery
- Consider the fabric composition and heat transfer vinyl compatibility for lasting prints.
- Play with different heat and pressure settings to find what brings out the best in your vinyl prints.
- Use Teflon sheets to prevent sticking and ensure precise temperature transfer.
Sublimation Strategies
- Keep a dust-free environment to prevent imperfections in your transfers.
- Experiment with sublimation ink and paper combinations for the best results.
- Time, temperature, and pressure are crucial in sublimation; get them right, and your prints will shine.
Innovative Techniques for Custom T-Shirt Printing
Exploring innovative methods can give your t-shirt prints that extra edge. This section dives into lesser-known techniques and equipment that can elevate your home-based printing game.
Creative T-Shirt Printing Equipment
- Laser Cutters: Use for creating custom designs out of fabric, especially in tandem with the traditional printing methods.
- 3D Printers: For the creation of unique accessories or enhancements for printed t-shirts.
- Unconventional Presses: Explore hat, shoe, and sleeve platen attachments for heat press machines.
Software and Digital Tools
- Design Software Add-Ons: Specialty add-ons can expand the capabilities of your existing design software.
- Online Platforms and Marketplaces: Utilize platforms to sell your custom designs or connect with other artists and expand your product offerings.
- Custom Apps and Tools: Develop or use apps that help streamline your design process or integrate with your printing tools.
Hybrid Techniques and Mixed Media
- Stenciling: Integrate stenciling with traditional or digital methods for unique textures and layers.
- Hand-Painting and Embellishing: Use fabric-safe paints and pens to add custom details to printed designs.
- Fabric Dye Submersion: Dip-dye or tie-dye sections of t-shirts to complement printed designs.
Overcoming Common Challenges in Home-Based T-Shirt Printing
Honing your craft at home comes with its fair share of hurdles. Here are proactive solutions to the most common challenges faced in t-shirt printing.
Ink and Print Quality Maintenance
- Store inks properly according to manufacturer guidelines to maintain consistency.
- Monitor ink levels and discard old inks to prevent issues.
- Regularly check and replace print heads on digital printers to avoid degradation of print quality.
Design Consistency and Reproduction
- Create and follow detailed production notes to ensure consistency in design elements.
- Conduct regular quality checks during the printing process to catch any deviations early.
- Keep color and size calibration tools handy for quick adjustments.
Equipment and Workspace Optimization
- Regularly upgrade and maintain your printing equipment to keep up with increasing demand and technological advancements.
- Organize and clean your workspace regularly to prevent accidents and to maintain a productive environment.
- Use space-saving solutions and multi-functional equipment to maximize your printing area.
In conclusion, home-based t-shirt printing is part science, part art, and entirely rewarding. Armed with the techniques discussed and a spirit of experimentation, the fabric of possibilities is within your grasp. Happy printing, and here's to the wearable stories you'll create!
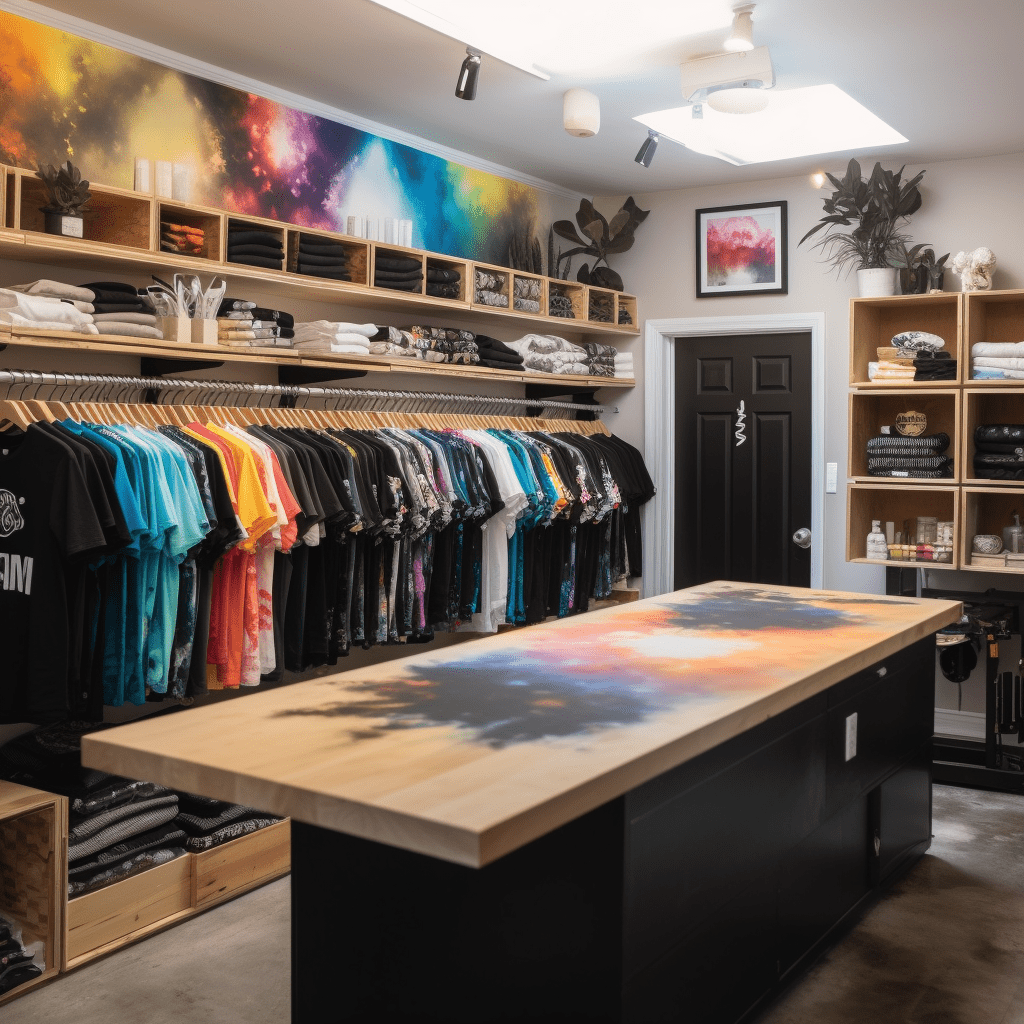